I have a most creative customer (Nelson) who is always thinking outside the box when it comes to jewelry design. His latest concept was a Upper Peninsula representative pendant with an Isle Royale Greenstone placed approximately where Isle Royale is located. Nelson was given the honor of naming this pendant which he called “Yooperland”, so for here on out they will be Yooperland Pendants.
After some thought Nelson decided on a U.P. cut from firebrick. Firebrick has been talked about in my blog before but let’s review: When the copper smelters were build in copper country, they were made of brick. Over the years as copper was smelted, the copper vapors and solids permeated into the brick and replaced everything except the silica materials. After the mines were closed the ovens and stacks were either taken down or fell down. Enterprising individuals then took away some of this heavy material and used it in lapidary projects. Today fire brick is quite scarce, but there are still stashes around. Since firebrick has such a great story of the Copper Country, it makes wonderful conversational jewelry.
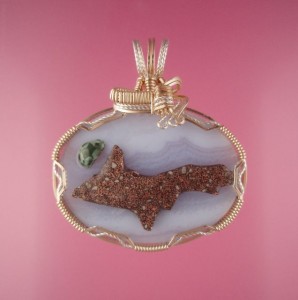
This "Yooperland" is a wonderful design.
I usually coat my firebrick jewelry with a two-part epoxy resin to prevent it from tarnishing. This will keep the “Yooper land” pendant shining with a coppery look.
I used a 30X40mm Blue Lace Agate cabochon as the base for this project. After cutting out the firebrick and prepping it, I polished a wonderful Greenstone. Both of those stones were glued to the Blue lace so it appears as if everything is floating in Lake Superior.
The wire wrapping in gold and silver is quite elegant as befitting Nelson’s Queen. I added additional height to the perimeter to protect the firebrick and the greenstone. I expect Nelson’s wife will have a wonderful birthday gift. She loves U.P. themed jewelry.
I expect to make several more of these before spring. I believe these pendants will be one of our most popular, especially for our U.P. shows.
Nelson wrote me after giving his wife her Yooperland: The YOOPER LAND pendant is OUTSTANDING! I gave it to my wife for her birthday and she loves it. However there is a small issue that I must deal with when we go out in public. Nearly everyone comments on her necklace- BUT the rest of the people just stare. Sometimes I get a little jealous . MAYBE the solution would be a turtle neck shirt!
By the way my wife says “THANKS”